What is preventive maintenance?
A proactive approach to maintenance that involves regularly scheduled inspections, maintenance tasks, and repairs aimed at preventing equipment failures and optimizing performance.
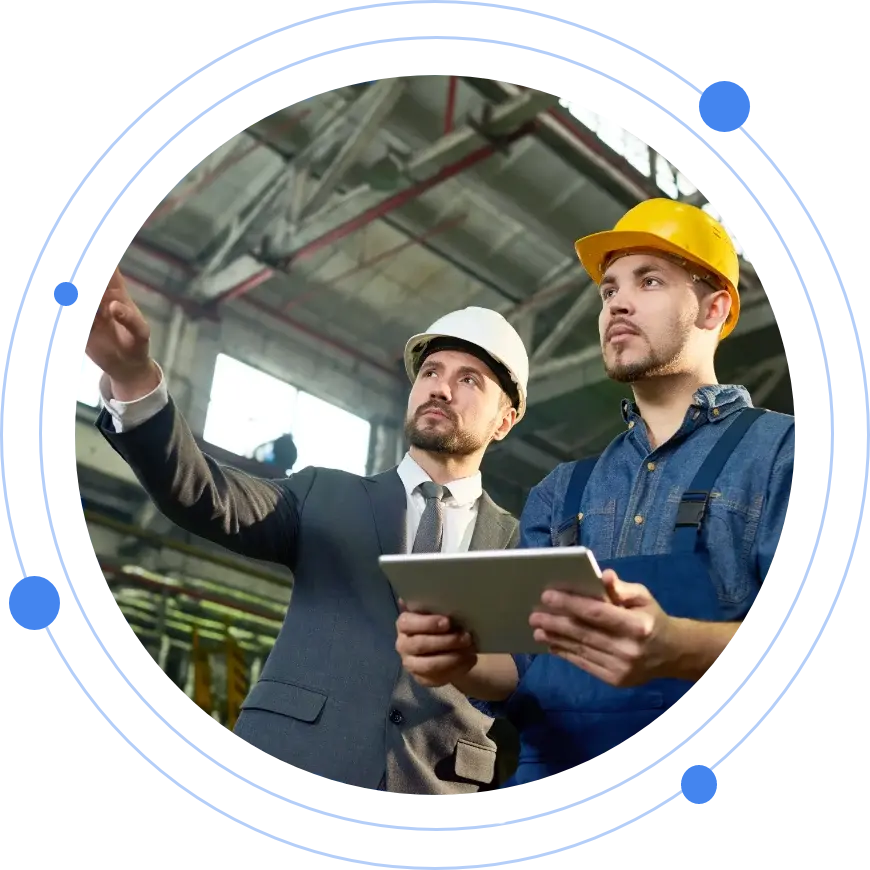
CMMS with AI
Integrations
Blog
A proactive approach to maintenance that involves regularly scheduled inspections, maintenance tasks, and repairs aimed at preventing equipment failures and optimizing performance.
Preventive maintenance is a proactive approach to maintenance that focuses on scheduled inspections, routine tasks, and preemptive repairs. Its primary goal is to prevent equipment failures, minimize downtime, and extend asset lifespan. Rather than waiting for equipment to break down, we identify and address potential issues before they cause major problems.
It includes regular inspections, lubrication, cleaning, calibration, and component replacements based on manufacturer recommendations or established intervals. By following a well-defined maintenance schedule, we can ensure equipment operates at optimal performance levels, reduce unexpected breakdowns, and avoid costly emergency repairs.
Preventive maintenance involves developing and implementing a comprehensive maintenance plan. This includes defining inspection criteria, creating maintenance checklists, establishing maintenance intervals, and assigning responsibilities to maintenance technicians. It's crucial to document all maintenance activities and keep accurate records to track equipment history, identify trends, and make data-driven decisions.
An effective preventive maintenance program requires collaboration with other departments, such as operations and production. This is done to schedule maintenance activities during planned downtime periods, minimizing disruption to operations. Additionally, it's essential to leverage technology, such as computerized maintenance management systems (CMMS), to streamline maintenance processes, automate work order generation, track asset performance, and generate reports for analysis.
It is a proactive strategy that aims to optimize equipment performance, minimize unexpected failures, and improve overall operational efficiency. By implementing a well-designed preventative maintenance program, we can enhance equipment reliability, reduce repair costs, and increase productivity and longevity of our assets.
Preventive maintenance plays a crucial role in ensuring our facility's smooth and efficient operation. It is not just an additional task to be performed; rather, it is a strategic investment in the reliability and longevity of our equipment and infrastructure. Let me explain why it is so significant:
By regularly inspecting and maintaining equipment, we can identify and address potential issues before they escalate into major breakdowns. This proactive approach helps us minimize unplanned downtime, which can disrupt production schedules, impact customer satisfaction, and result in costly emergency repairs.
Properly maintained equipment has a longer operational life. Regular maintenance activities, such as lubrication, cleaning, and component replacements, reduce wear and tear, prevent premature failure, and ensure optimal performance. This, in turn, maximizes the return on investment (ROI) for our assets and avoids untimely and costly replacements.
A comprehensive preventative maintenance program enhances workplace safety. Regular inspections and maintenance activities help identify and rectify potential safety hazards, such as faulty wiring, leaks, or worn-out safety devices. By proactively addressing these issues, we create a safer work environment for our employees, contractors, and visitors.
Although implementing preventative maintenance requires upfront investment in terms of time, resources, and manpower, it ultimately leads to significant cost savings in the long run. By identifying and addressing minor issues early on, we can prevent them from escalating into major failures that are more expensive to fix. Additionally, routine maintenance tasks are often less time-consuming and costly than emergency repairs.
Well-maintained equipment operates more efficiently, resulting in optimized production processes, reduced energy consumption, and improved overall efficiency. Regular calibration, cleaning, and lubrication ensure equipment performs at its peak, minimizing energy waste and maximizing output.
Many industries have specific maintenance requirements mandated by regulations and standards. Implementing preventative maintenance helps us meet compliance requirements, avoiding penalties, legal issues, and reputational damage.
Through proper documentation and record-keeping of maintenance activities, we can gather valuable data over time. This data enables us to identify trends, track asset performance, and make informed decisions regarding repair versus replacement. It also optimizes maintenance schedules.
By emphasizing the importance of preventative maintenance, we can establish a culture of proactive asset management. This will increase equipment reliability and improve operational efficiency. It is an investment that pays off in terms of reduced downtime, increased equipment lifespan, enhanced safety, cost savings, and improved productivity.
To effectively perform preventative maintenance, it is critical to establish a structured and systematic approach. Here's a step-by-step guide on preventive maintenance:
Begin by identifying all equipment and assets that require preventative maintenance. Create a comprehensive inventory that includes essential details such as equipment name, model number, serial number, location, and criticality.
Develop a maintenance plan that outlines the specific tasks, frequencies, and intervals for each piece of equipment. Refer to equipment manuals, manufacturer recommendations, and industry best practices to determine appropriate maintenance activities. Consider factors such as operational requirements, environmental conditions, and regulatory compliance.
Create a maintenance schedule that specifies when each task needs to be performed. Determine the frequency based on factors like equipment usage, criticality, and historical performance. Assign responsibilities to qualified maintenance technicians, ensuring they have the necessary skills and resources to perform the tasks effectively.
Regularly inspect the equipment to identify signs of wear, damage, or potential issues. This can involve visual inspections, measurements, tests, or specialized equipment. Lubrication is a critical preventative maintenance task to ensure the proper functioning of moving parts. Follow manufacturer guidelines regarding lubrication types, quantities, and intervals.
Clean equipment regularly to remove dust, debris, and contaminants that affect performance. Use appropriate cleaning methods and agents that do not damage equipment. Calibration of instruments and controls should be performed according to a predetermined schedule to maintain accuracy and reliability.
Components with a limited lifespan, such as filters, belts, seals, and bearings, should be replaced as part of preventative maintenance. Refer to maintenance manuals or historical data to determine replacement intervals. Ensure that only high-quality, recommended replacement parts are used.
Maintain comprehensive documentation of all preventative maintenance activities. Record details such as date, time, task performed, technician responsible, and any observations or findings. This documentation helps track maintenance history, identify patterns, and supports data-driven decision making.
Regularly evaluate your preventive maintenance program's effectiveness. Analyze equipment performance data, maintenance records, and technicians' feedback to identify areas for improvement. Adjust maintenance tasks, frequencies, or procedures as needed to optimize the program.
Provide appropriate training to maintenance technicians on preventative maintenance procedures, safety protocols, and equipment-specific requirements. Foster open communication channels to encourage reporting of equipment issues or improvement suggestions.
Remember, preventative maintenance is an ongoing process that requires commitment, attention to detail, and continuous monitoring. By diligently following these steps and adapting the program based on feedback and performance data, we can ensure that our equipment remains reliable, downtime is minimized, and the lifespan of our assets is maximized.
Let's compare preventive maintenance with other maintenance approaches to understand their differences and benefits:
Reactive maintenance, also known as run-to-failure or breakdown maintenance, involves addressing equipment issues only when they occur. With this approach, maintenance actions are taken after a failure or breakdown has happened. While reactive maintenance may seem cost-effective in the short term, it has several drawbacks. It often leads to unplanned downtime, higher repair costs, potential safety hazards, and disruption to operations.
In contrast, preventative maintenance takes a proactive approach by regularly inspecting and maintaining equipment to prevent failures before they occur.
Predictive maintenance relies on data and technology to anticipate when maintenance actions should be performed. It involves monitoring and analyzing equipment performance using various techniques such as sensors, condition monitoring, and data analytics. By tracking key indicators and patterns, predictive maintenance aims to identify early signs of potential failures and trigger maintenance activities at the optimal time.
While predictive maintenance offers advantages in terms of cost savings and targeted maintenance interventions, it requires advanced monitoring systems, data analysis capabilities, and specialized expertise. Preventive maintenance, on the other hand, offers a simpler and more accessible approach that is widely applicable across different industries and equipment types.
Compared to reactive maintenance, preventative maintenance offers several advantages. It helps us minimize unexpected breakdowns, extend equipment lifespan, improve safety, increase efficiency, and save money. Predictive Maintenance has its merits, it often requires significant investments in technology and expertise.
Preventive maintenance, on the other hand, is a practical and widely applicable strategy that can be implemented with our organization's resources and expertise.
In summary, by implementing a well-designed preventive maintenance program, we can achieve a balance between proactive intervention and cost-effective maintenance. It allows us to prioritize maintenance activities, optimize equipment performance, and minimize disruptions, ensuring our assets' reliability and longevity.
While preventative maintenance offers numerous benefits, it is worthwhile to know potential challenges and drawbacks that may arise:
Implementing a comprehensive preventative maintenance program requires an upfront investment in time, resources, and manpower. It involves developing maintenance plans, creating schedules, training technicians, and establishing documentation and record-keeping systems. Preventive maintenance can be expensive, especially for organizations with limited budgets or complex equipment.
Preventive maintenance can sometimes create additional maintenance overhead. Scheduling and performing routine maintenance tasks takes time and resources away from other operational activities. It may require dedicated personnel or additional training for existing staff. Balancing preventative maintenance with other maintenance and operational priorities can be challenging, especially during peak production periods.
Preventive maintenance is based on predefined maintenance intervals and tasks. However, these intervals may not always align perfectly with the actual equipment condition.As a result, there is a risk of performing unnecessary repairs and maintenance actions based on false alarms. This can lead to wasted resources, increased maintenance costs, and potential disruption to operations.
Despite regular preventative maintenance, some equipment failures or deterioration may occur between scheduled maintenance intervals. Depending on the criticality and complexity of the equipment, unexpected issues are always possible. This highlights the importance of having contingency plans, reactive maintenance capabilities, and a responsive maintenance team to address unforeseen situations.
Effective preventative maintenance relies on strict adherence to maintenance schedules, tasks, and procedures. It requires discipline and a compliance culture within the maintenance team. Any lapses or negligence in following established preventive maintenance practices can compromise the effectiveness of the program. This can lead to missed opportunities for identifying potential issues.
While preventive maintenance is a valuable approach, it may not be the most efficient strategy for all types of equipment or assets. Certain critical systems may require more advanced maintenance methods, such as predictive maintenance or condition-based monitoring, to detect subtle changes or faults that may not be visible during routine preventative maintenance checks. Therefore, it is critical to assess the specific needs of different equipment and consider alternative maintenance strategies where appropriate.
It's crucial to acknowledge these potential challenges and proactively address them. Regular evaluation, continuous improvement, and a data-driven approach can help optimize preventative maintenance efforts and mitigate negative aspects. By striking the right balance and addressing these challenges, we can ensure that preventative maintenance remains a valuable tool in our maintenance management toolkit.
There are various types of preventive maintenance approaches depending on the specific needs and characteristics of the equipment or assets. Let's explore some common types.
Time-based maintenance involves performing maintenance activities at predetermined intervals based on time. These intervals are typically established by equipment manufacturers' recommendations, industry standards, or internal organizational guidelines. Time-based maintenance focuses on regularly scheduled inspections, lubrication, cleaning, and component replacements.
This approach assumes that equipment deterioration occurs over time, regardless of usage or condition. It is a common, straightforward type of preventive maintenance that ensures routine equipment maintenance.
Usage-based maintenance, also known as meter-related or run-time maintenance, considers the actual operating hours or usage of the equipment as the basis for maintenance intervals. Monitoring systems or hour meters track equipment runtime, and maintenance tasks are scheduled depending on predetermined thresholds.
For example, a maintenance task may be triggered after a certain number of production cycles or operating hours. Usage-based maintenance is particularly useful for assets with varying workloads or equipment that experiences wear and tear primarily depending on usage rather than time.
This approach relies on real-time monitoring and assessment of equipment condition to determine when maintenance activities are required. It involves utilizing various sensors, data collection, and advanced monitoring techniques to detect early signs of equipment deterioration or abnormalities.
By continuously monitoring key indicators such as vibration, temperature, pressure, or fluid levels, maintenance tasks are performed only when specific conditions or thresholds are met. CBM allows for more targeted and efficient maintenance actions, as tasks are performed based on the actual condition of the equipment rather than predetermined schedules.
Reliability-centered maintenance (RCM) is a comprehensive approach that involves analyzing and optimizing maintenance strategies based on equipment failure criticality and consequences. RCM aims to identify the most effective and efficient maintenance tasks for each piece of equipment. It involves detailed failure modes analysis, root cause analysis, and risk assessment.
By understanding the potential failure modes and their impact on operations, RCM helps prioritize and tailor maintenance activities to maximize reliability and minimize costs.
In certain cases, preventive maintenance may involve proactive replacement or renewal of components or systems based on their expected lifespan or known failure rates. This approach ensures that critical parts are replaced before they fail and cause disruption.
Proactive replacement or renewal can be determined through historical data, industry best practices, or analysis of specific failure patterns.
It's critical to note that these types of preventative maintenance are not mutually exclusive. They can be combined based on the needs of the equipment and the organization. A well-designed preventative maintenance program may incorporate elements of multiple types to create a comprehensive and effective maintenance strategy.
By understanding the different types of preventive maintenance and their applicability, we can tailor our approach to maximize equipment reliability, minimize downtime, and optimize maintenance resources.
Developing a comprehensive preventative maintenance strategy requires careful planning and consideration of various factors. Here's a step-by-step approach to building an effective PM strategy:
Begin by creating an inventory of all your equipment and assets.Assess the criticality of each asset by considering factors such as its impact on operations, safety risks, downtime consequences, and maintenance history. This will help prioritize which assets require more frequent and rigorous preventative maintenance.
Review equipment manufacturer documentation, manuals, and guidelines to understand their recommended maintenance tasks, intervals, and specifications. Additionally, research industry best practices to gain insights into commonly accepted maintenance standards and practices for similar equipment types.
Identify the specific maintenance tasks required for each asset based on the criticality assessment, manufacturer recommendations, and industry practices. This includes tasks such as inspections, lubrication, cleaning, calibration, and component replacements. Clearly define the scope, frequency, and procedures for each task.
Develop a maintenance schedule that specifies when each task should be performed. Consider factors such as equipment usage, production schedules, and operational requirements. Determine the frequency of maintenance tasks based on asset criticality, historical performance, and industry standards.
Assess the resources required to execute the preventive maintenance strategy effectively. This includes manpower, tools, spare parts, and any additional equipment needed. Ensure that you have the necessary resources available and properly allocated to perform maintenance tasks within the scheduled time frame.
Establish a system for documenting all maintenance activities and maintaining accurate records. This includes creating work order templates, checklists, and forms for each maintenance task. Implement a computerized maintenance management system (CMMS) or similar software to track and manage maintenance activities, equipment history, and generate reports for analysis.
Provide training and skill development opportunities for your maintenance team to ensure they have the knowledge and expertise required to perform preventive maintenance tasks effectively. This includes technical training on specific equipment, safety protocols, and maintenance procedures.
Regularly evaluate your preventive maintenance strategy's effectiveness. Analyze equipment performance data, maintenance records, and technicians' feedback to identify areas for improvement. Consider feedback from operators and other stakeholders to refine the strategy and adjust maintenance intervals or tasks as needed.
Foster collaboration between maintenance, operations, and other departments to ensure effective implementation of the preventive maintenance strategy. Communicate the importance of preventative maintenance to stakeholders, management, and employees to gain their support and cooperation.
Remember, a preventative maintenance strategy is not static. It should be continuously reviewed, refined, and improved to adapt to changing equipment needs and organizational goals. By following these steps and maintaining a proactive and data-driven approach, you can develop a preventive maintenance strategy that maximizes equipment reliability, minimizes downtime, and optimizes your assets' performance
Maintenance software, such as a computerized maintenance management system (CMMS), supports and enhances preventive maintenance efforts. Here's how maintenance software can help with PM:
In summary, maintenance software simplifies and streamlines preventive maintenance activities. It enhances efficiency, improves communication, and provides valuable data for optimizing maintenance strategies. By leveraging maintenance software, you can strengthen your preventive maintenance program, increase equipment reliability, and achieve better overall maintenance outcomes.
Manufacturing plants need preventive maintenance to minimize production disruptions and optimize equipment performance. For example:
Healthcare facilities need preventive maintenance to ensure medical equipment reliability and patient safety. Some use cases include:
Preventive maintenance is vital to keep vehicles and infrastructure safe and operational. Examples include:
In power generation plants or renewable energy installations, preventive maintenance is essential to avoid costly downtime and maintain efficient operations. Use cases include:
In commercial buildings or facility management, preventive maintenance helps maintain a safe and comfortable environment for occupants. Some use cases include:
These use cases demonstrate the wide-ranging applications of preventive maintenance across different industries. By implementing proactive maintenance strategies, organizations can minimize downtime, extend asset life, enhance safety, and improve overall operational efficiency.
Here are some frequently asked questions (FAQs) related to preventive maintenance: